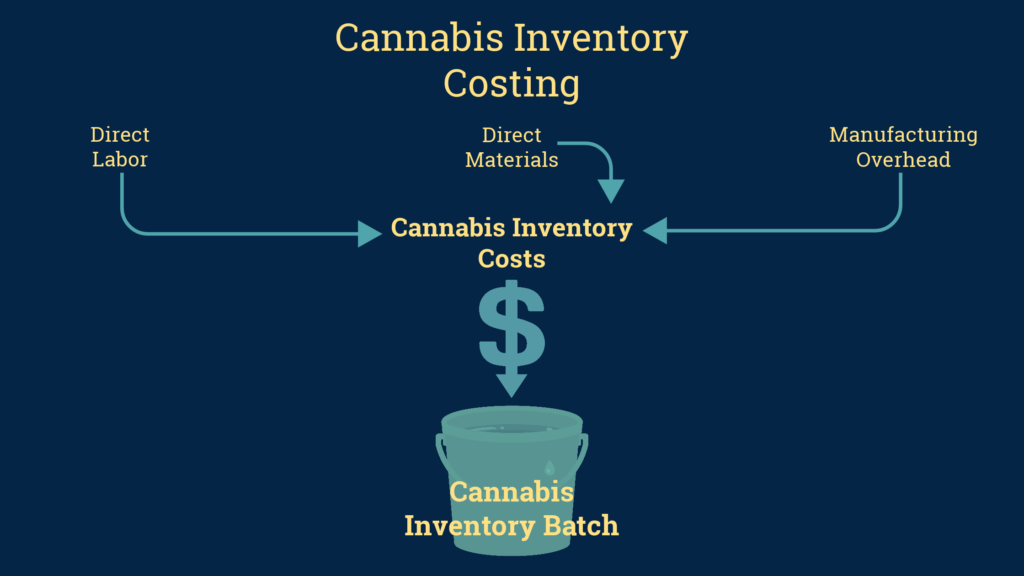
A wise CFO once tried to explain to me how he wanted costs associated with the cultivation and production of cannabis good recorded. He described “buckets” that the costs would essentially “go into”. Thus began my journey of researching cannabis inventory costing. What are these theoretical buckets? What costs “go into” these buckets? How do we determine these costs? These were the questions I needed answers to. It wasn’t long before I understood what he was trying to teach me, and how it applies to the cannabis industry. Specifically, how cannabis inventory costing applied to the cannabis cultivation, manufacturing, and retail operations.
Cannabis Inventory Costing by Batch
Batch costing is the process of allocating costs associated with a particular batch to get a total batch cost. Next, the total batch cost is divided by the number of units in the batch which results in the cost per unit. Each batch can be thought of as a “bucket” which accumulates costs. Thus, the CFO was talking about batches when he was referring to “buckets” while explaining cannabis inventory costing.
Cannabis Inventory Costs
I wish cannabis inventory costing were simple. It would make identifying all costs associated with each batch relatively easy. None the less, we can identify 3 categories of costs that should be allocated to each batch of cannabis. These categories include direct materials, direct labor, and direct overhead.
Direct Materials
Direct materials are materials used in the cultivation or production of cannabis and cannabis products. Such materials might include nutrients, soil, packaging, and any ingredients used in the production of cannabis products. Direct material costs for each batch can be tracked in some seed to sale software systems.
Direct Labor
Direct labor is the labor directly associated with the batch. Including, vegetation staff, cultivation staff, trim labor, and packaging labor. It is important to have a seed to sale system that has the capability of tracking the amount of time a plant spends in each stage of the cultivation and production process. The time in each stage will help determine the direct labor rate to apply to each batch. Because, each batch’s direct labor cost will differ.
Manufacturing Overhead
Overhead costs are costs that cannot be directly associated with a particular batch. Such costs may include electricity, water, and rent or mortgage. These numbers will also depend on how much of the facility is used directly in cultivation and processing VS how much of the facility is used for administrative and sales purposes.
To explain, if a 1,000 square foot building contains 250 (25%) square feet of administrative purposes, and 750 (75%) square feet of cultivation and processing, only 75% of the electricity, water and rent would be included in the manufacturing overhead amount. This amount may be divided among the batches in production. The other 25% of the rent, electricity, and water would be included in the facility overhead, or cost of goods sold amount.
How to Determine These Costs
Tracking the costs associated with each batch of cannabis requires at least 3 things. An understanding of the costs and where they come from, a good seed to sale inventory tracking system, and lastly standard operating procedures. Fortunately, we can recommend good seed to sale systems. Additionally, we have Standard Operating Procedures that can assist you with identifying when costs are accumulated and how to record them. These documents are state specific because we understand that every state has different cannabis requirements.
We want to help you track your cannabis inventory costing and implement processes to continually track costs. Contact us today to schedule a consultation.